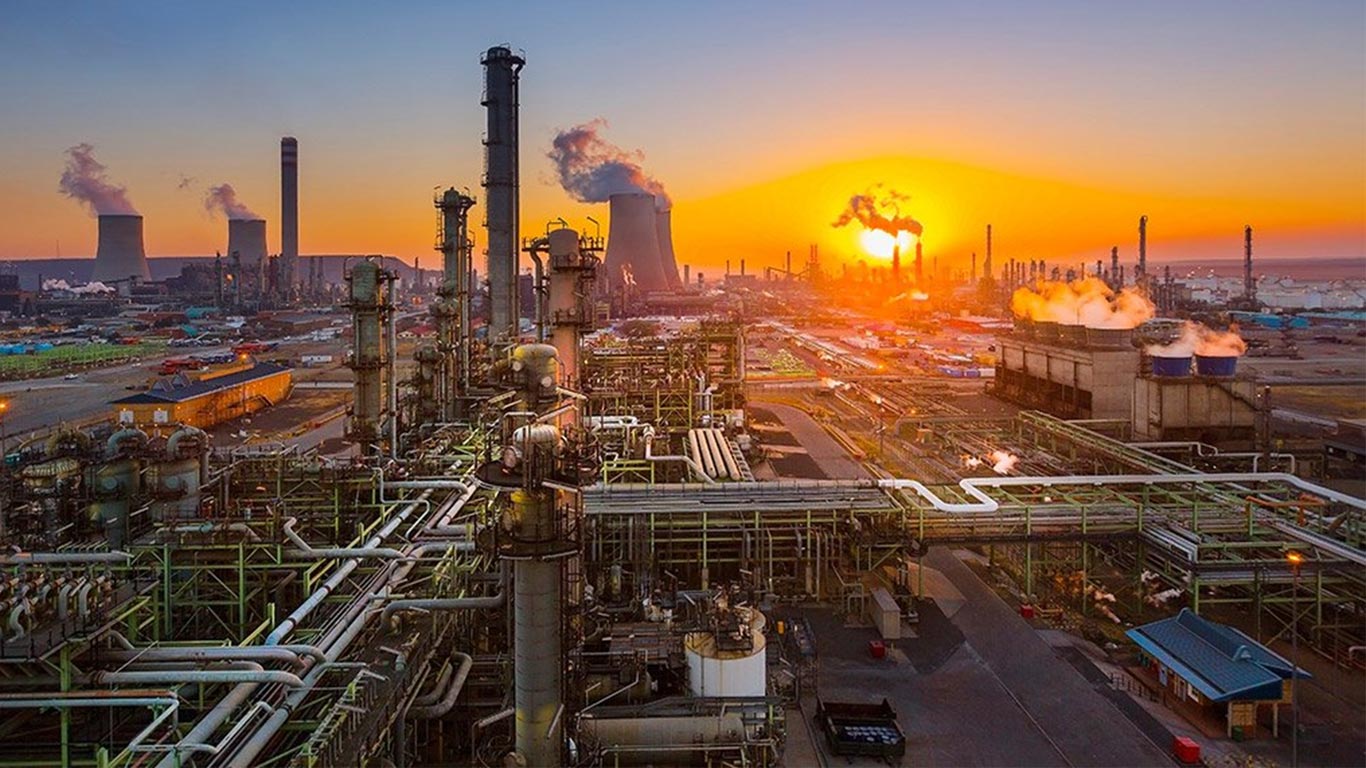
NEW SYNCHRONOUS TOPOLOGY BY POLYWAVEPOWER CHALLENGES THE INDUCTION MOTOR
ELECTRO-MAGNETIC BREAKTHROUGH!
Stationary Field Synchronous Motor.
Without slip rings, permanent magnets or high-powered computer electronics, this new topology delivers improved efficiency PLUS Unitary Power Factor correction.
Potential Impact
- a greatly improved more efficient industrial motor,
- low mass wind turbine generator,
- easily cooled turbo‐generator and
- high reliability marine motor/generators.
Inventor: Dragan Ignjatovic, PolyWavePower, South Africa
Historically, the 3-phase synchronous motor and the 3-phase asynchronous induction motor were invented virtually together in the last decade of the 19th Century. However, the induction motor surged ahead to become the de facto industrial motor of the 20th Century as it could be made reliably at a low cost without slip rings. The synchronous motor requires slip rings to supply DC current to the field coils on the rotor. The 3-5% slip of the induction motor was considered acceptable. The synchronous motor remains today a highly efficient motor built for specialist applications, including power factor (PF) correction and variable speed control. They are considerably more expensive than their equivalent induction motors and, for that reason, have not penetrated the broad industrial workplace.
The efficiency limitations of the induction motor became a challenge by the end of the 20th Century and developers worked on improving their efficiency by building high power drivers. Others worked on an older synchronous reluctance topology and again, with the assistance of high-power drivers, were able to develop a high-performance motor for industrial and mobile platforms. However, in both cases, these developments came with a cost and a reliability penalty that was not compensated in anyway by an improvement in the power factor of the motor. These motors have presented the industry with a dilemma in that they are considered too capital intensive. There is customer resistance to specifying them unless demanded by Regulations.
At a high level, the present invention aims to provide a stationary field synchronous motor typology, to address manufacturing costs and improve operational efficiency, and that does not require the use of slip rings, permanent magnets and high-power electronic drivers. This allows full power factor control of the motor under all load conditions for near ideal efficiency. The improved power factor in turn means more grid capacity and a reduction in PF penalties imposed by the generation companies. Grid operators will benefit too by having more stable networks, all of which can be achieved without the introduction of capacitor banks and spinning condensers. Additional objectives of the present invention is to enable the motor to be line-started using induction rings placed in either the rotor or the stator, thereby providing further design flexibility. In addition, the proposed synchronous motor typology can use low power field control suitable for highly reliable use in industrial motor applications, thereby improving motor flexibility and performance under arduous working conditions. It is envisaged that these combined cost saving benefits will ensure a relatively rapid conversion to the low-cost synchronous motor of the present invention and a phasing out of the induction motor after its 130 years of dominance.
World Class Efficiency
IE5 and IE6 for industrial Motors & Generators.
Low Production Cost
Manufactured at IE3 induction
motor cost.
AC or DC Source
No inverter or converter required.
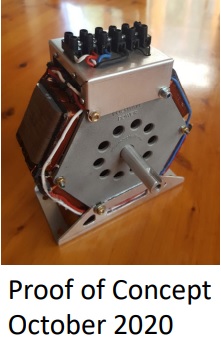
SUMMARY OF ADVANTAGES
Three unique Performance Advantages
PolyWavePower is a patented synchronous motor topology developed in South Africa and now patent‐filed in 8 manufacturing regions around the world. It sets itself apart by having three unique performance advantages over other motor topologies including the dominant induction motor and the favoured synchronous reluctance motor.
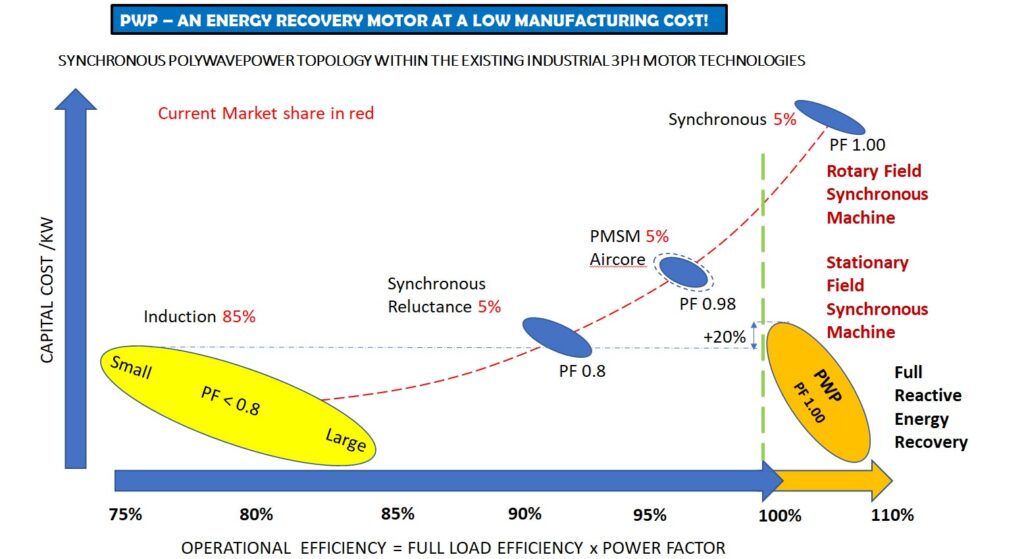
1. Stator‐based Field Coil
The first advantage is in its patented topology that employs a stator‐based field coil to excite and fully control the magnetization of the salient poles of the rotor. The rotor is therefore free of field windings and slip rings, low in mass, cool‐running and maintenance‐free. This is a unique achievement and a major advancement over existing wound rotor or Permanent Magnet synchronous motors.
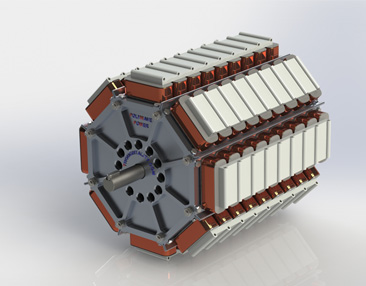
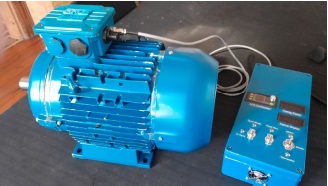
2. Optimised efficiency under all load conditions
Advanced Low Power Management is now possible, using the Power Factor correcting features of this motor. The
efficiency of the motor is optimised under all load conditions, thereby raising the whole Plant’s Power Factor
Performance resulting in a reduced cost of Grid energy.
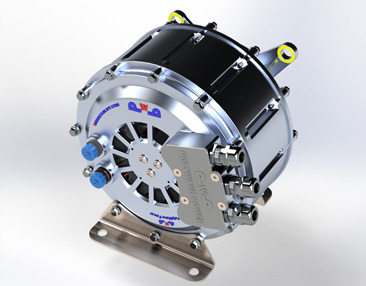
3. No computer aided High‐Power Electronics needed to produce a synchronous motor using AC or DC current
Advanced High‐Power Electronics is not required for the line starting or running of these motors. PolyWave motors are simple to manufacture and can be readily optimised to AC or DC power sources using less inversion and conversion electronics. This is an advantage when using either Batteries or Fuel‐cells as the power source.
CONCLUSION
An industrial motor has to be strongly constructed, long‐lasting, electrically robust, reliable and be able to
withstand very harsh operating conditions.
At the same time it should not be too expensive, have a low maintenance cost and be possible to repair with
standard workshop tools.
This is a challenging set of roles to fulfil and the induction motor has, for this reason, reigned for over 130
years.
With the PolyWavePower topology, all of the above can be achieved, and more.
1.) Without using high‐power electronics. A substantial cost saving.
2.) PWP goes significantly further to raise the Power Factor of a whole Plant to near ideal Power Management levels. This justifies rapid conversion from induction to PWP motors.
3.) PWP goes even further to introduce new solutions for the use of DC on mobile platforms and variable DC generation sites that can reduce mass and increase reliability.
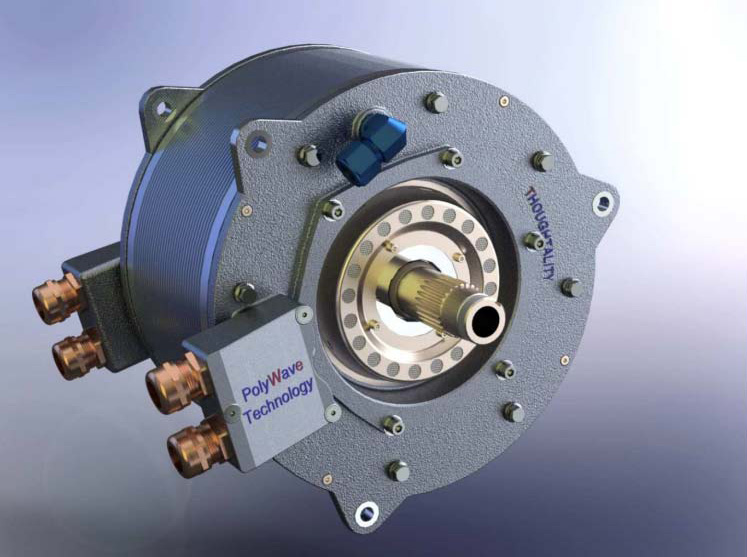
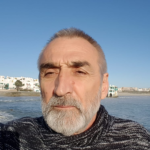
“Engineering success is surviving the arduous path to simplicity”
Dragan Ignjatovic
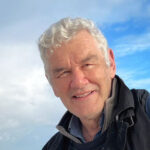
“Astounding energy capture, and sustainability”
Mark Simpson
Stationary Field Synchronous Motor.